Brake Caliper Manufacturing

Step 1
Creating a manufacturing batch
When we create a production batch we go through a number of processes to ensure everything is ready before the batch hits the shop floor. Our production engineering team assess the manufacturing drawings, production routing, material, tooling, and machine programs to ensure a smooth process.Step 2
Ensuring Full Traceability
We normally use 7075-T651 aerospace grade aluminium for our caliper bodies. Our approved suppliers deliver the material in billet form with a certificate of conformity right back to the mill where it was produced and the specific batch that is was produced on. On receipt of the material we mark the billets with the traceable numbers and these are machined into the caliper during production. If a customer returns a caliper at any time we can trace it back to the mill to confirm the material was correct and isolate any calipers made with that material.
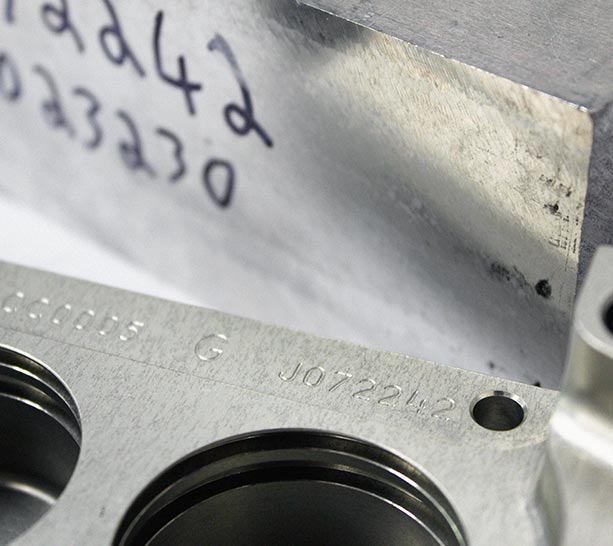

Step 3
Computer Aided Manufacturing Process
Our CNC machines are programmed by dedicated CAM engineers using the latest Edgecam software.
Step 4
CNC Machining
Using a suite of HAAS 3 and 5 axis high speed machining centres we machine our calipers to the very highest standards.
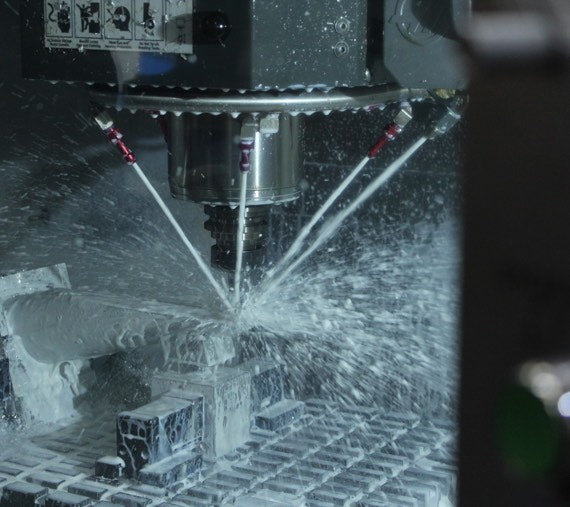
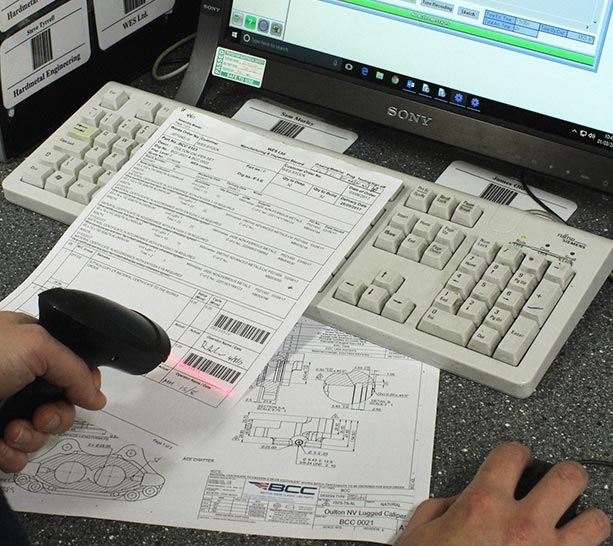
Step 5
Clocking and Scanning
We have a rigorous shop floor data collection (SFDC) process to ensure we continually improve our processes and have up-to-the-minute tracking of production batches. If your caliper is being made to order we can tell you exactly where we are in the process and how much machining time is left.
Step 6
Final Inspection
Once the machining process is complete all of our caliper bodies are inspected using a variety of inspection techniques and equipment including CMM measurements of the key dimensions to an accuracy of 5 microns.
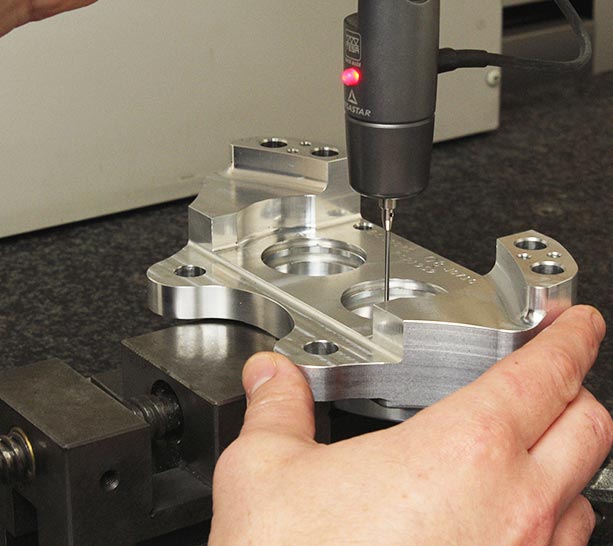

Step 7
Anodising
Calipers are sent to an approved anodising supplier who sulphuric anodise the calipers all over which protects the aluminium from corrosion. We offer a wide choice of caliper colours! Black and Silver are the most popular colours and are usually held in stock but you can also have blue, red, yellow, green, purple, orange or even gold! It takes 2 - 3 weeks to prepare a colour other than black or silver.
Step 8
LASER MARKING
We can laser mark various artwork onto your caliper, normally our BCC logo, or we can leave it plain. If you’re a restoration business or a parts business selling our calipers we can laser mark your company logo onto the calipers. If you’re an individual and want your own artwork give us a call to discuss the options.
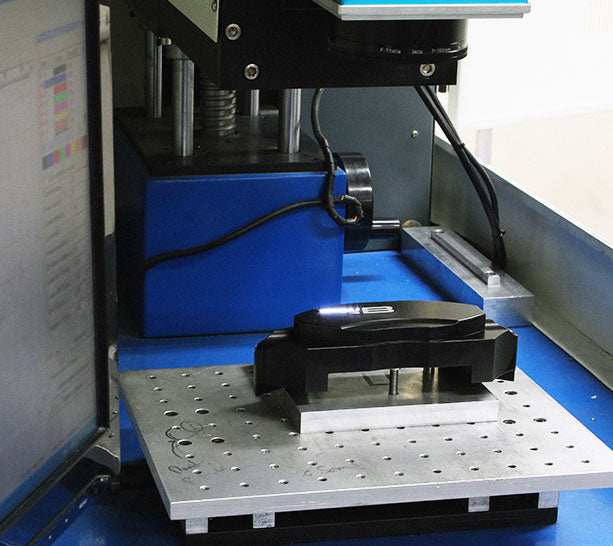
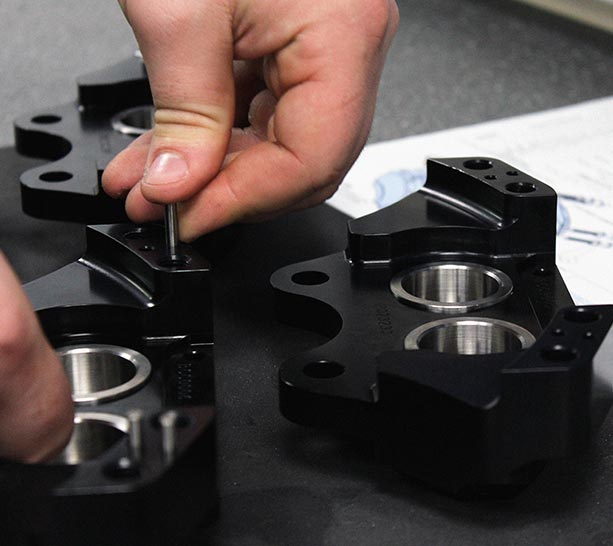
Step 9
Assembly
We normally only assemble calipers once a customer places an order so they can select the colour, artwork and assembly components of their choice. We have several highly skilled assembly staff that use our dedicated caliper assembly area with various checks to ensure nothing is missed.
Step 10
External Components
Brake pads from EBC or Mintex, the highest quality pipes and adaptors from Automec, modern fluid and dust seals from Liberty, and specialist high specification Holokrome bolts. We take great care in selecting only the best quality assembly components that compliment our calipers.

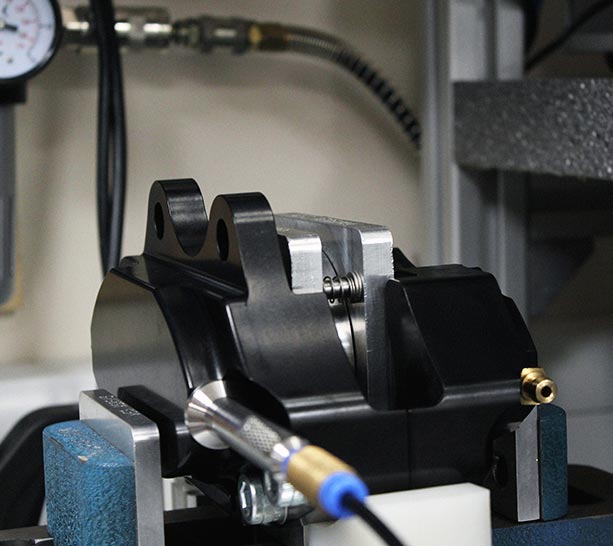
Step 11
Testing
We test every caliper we produce using our dedicated pneumatic test rig which pressurises the caliper and monitors any reduction in the pressure to identify any leaks. The software will tell us if the caliper passes or fails the test and if it passes it will produce a certificate that we include in the box.
Step 12
Boxing
We carefully pack your new brake kit into bespoke boxes to ensure they are received in pristine condition.
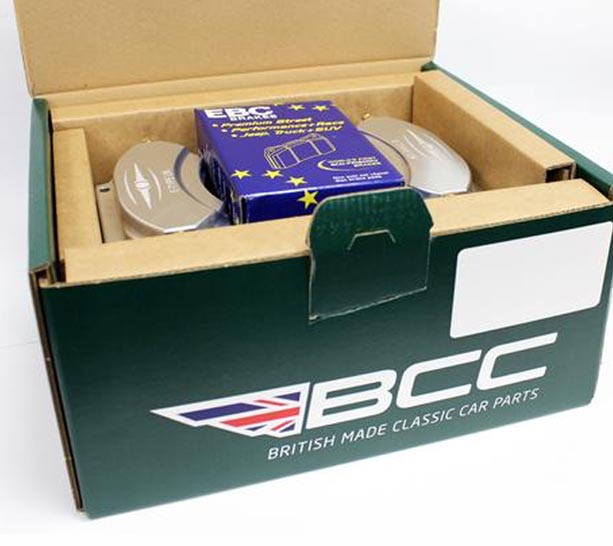