Suspension Manufacturing
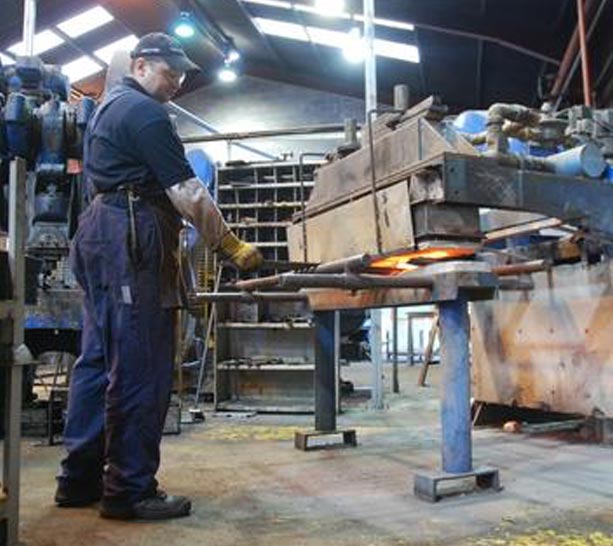
Step 1
British Steel
BCC Leaf springs are made from British steel and manufactured to an exact standard using an ISO 9002 quality control system to maintain a consistently high standard production processes.Step 2
Cutting
The steel is cut to the correct length with the correct end profile which is often tapered or chamfered. Various widths and thicknesses of steel are used to match the original specification wherever possible.
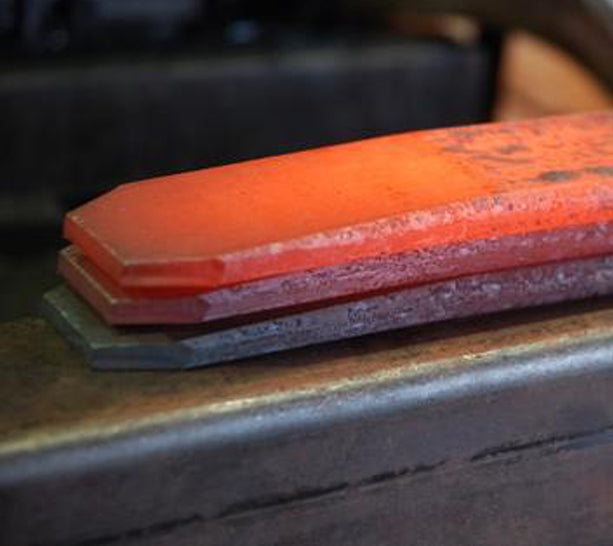
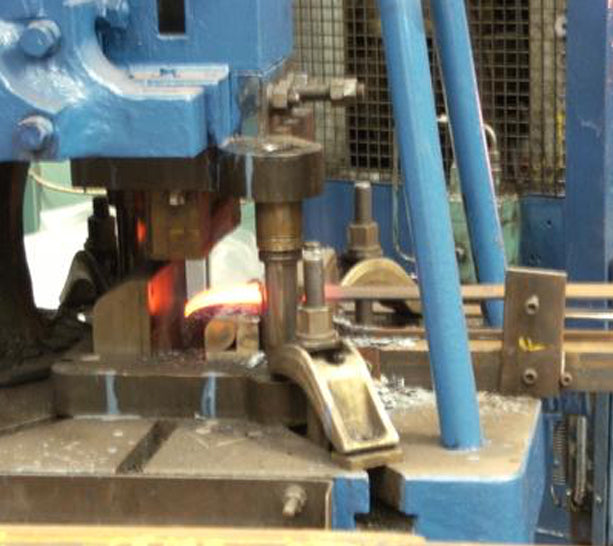
Step 3
Bending
The steel is then bent into shape. This is carefully calculated to ensure we match the ride height and 'feel' of the car when it's driven.
Step 4
Forming the eyes
The eyes are formed with a diagonal cut on the steel, then heated, then the initial curl is performed followed by more heat and then the full roll is completed.

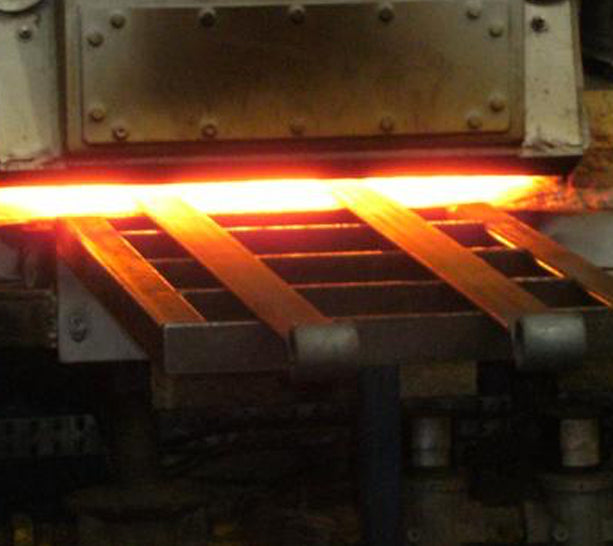
Step 5
Heat treatment tempering
Heat treatment is undertaken within strict guidelines to ensure optimum hardness and ultimate performance.
Step 6
Quenching
The steel is rapidly cooled by quenching is water to ensure the material properties are maintained.
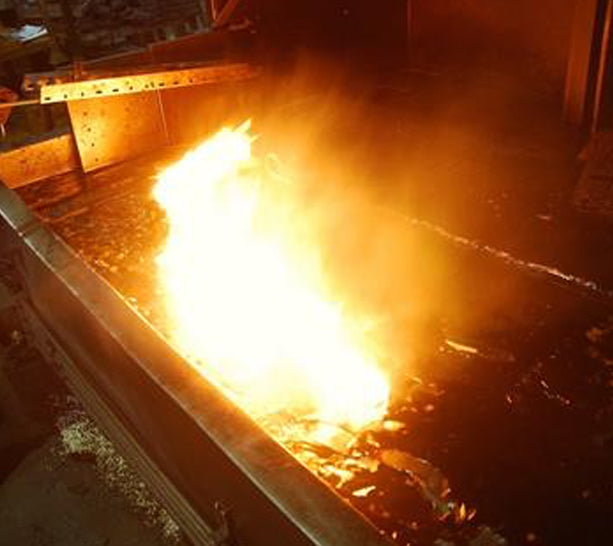
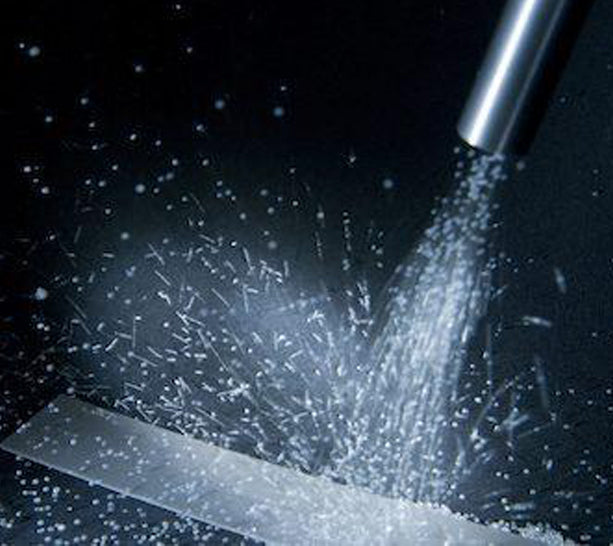
Step 7
Shot peening
The leaves are shot-peened to give a long fatigue life.
Step 8
Painting
Special black anti-corrosion paint is used to preserve the steel and give the springs a good visual appearance.
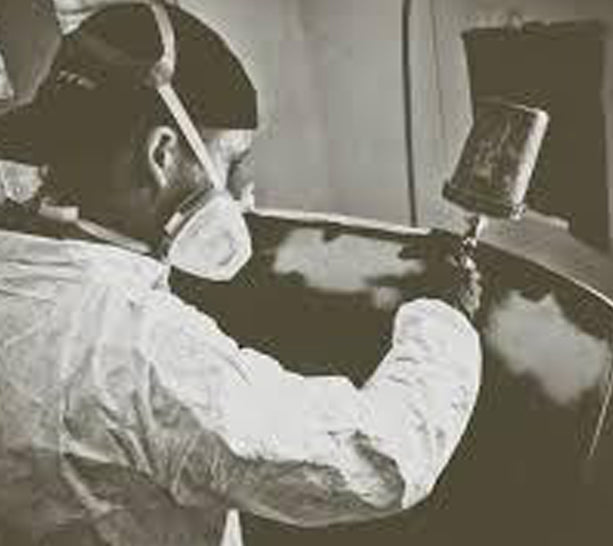
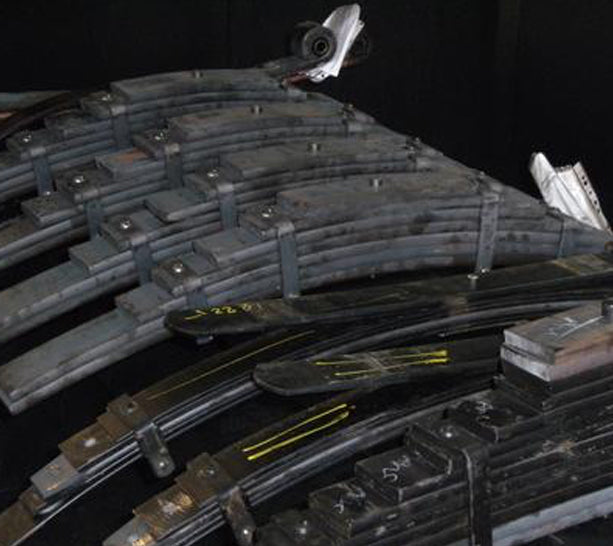
Step 9
Assembly
Our range of multi-leaf semi elliptic springs are assembled to the manufacturer’s original specification wherever possible including the appropriate inter-leaving, wear pads, clips, and buckles.
Step 10
Testing
All of our leaf springs go through a rigourous testing procedure to ensure they comply with the specification.
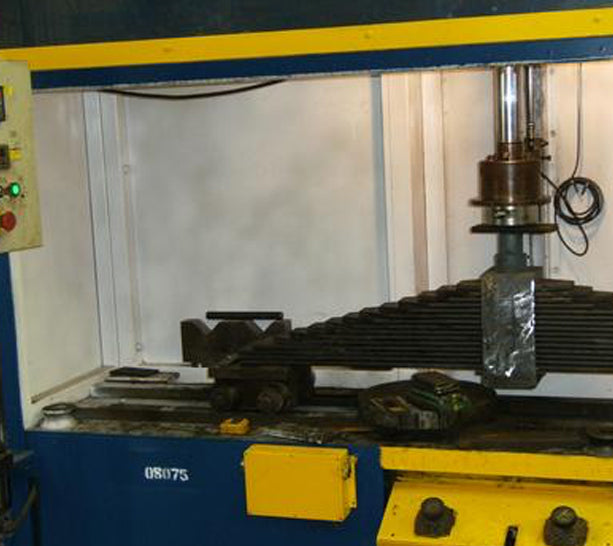